Alex Lau
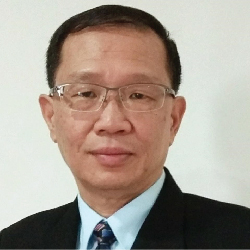
On-demard Webinars by Expert
Creep Failure of Molded Plastic Parts and Design Guidance
Speaker: Alex Lau
Registration Fee: Member: 225 US$
Non-Member: 375 US$
Group (5 Pax): 900 US$
Non-Member: 375 US$
Group (5 Pax): 900 US$
Language: English
Time Length: ~85 Min
To Register: Details & Register
Description: Creep failure of plastic parts is the permanent deformation of the part in the presence of stress, time, and temperature. Plastics are more prone to creep failure than metals. Because creep failure only manifests itself after time has passed it is usually the customer who experiences it. This has the potential for costly recalls, returns, rework, warranty claims, loss of reputation, etc. And the correction will take a long time to implement because it likely involves a redesign, re-tool and mold, re-test, which prolongs the customer’s pain. Merely replacing the failed part with one of the same vintage will repeat the pain. This webinar will discuss how to identify potential creep failure of plastic parts, and how to design around them.
Speaker: Mr. Alex Lau holds a B.Sc. in Mechanical Engineering from University of Manchester, and has worked in the R&D’s of several prominent global MNC’s (Novatel Calgary, NORTEL Calgary, Motorola Penang, Agilent Penang, and Seagate Seremban). He has >30 years experience, specializing in the design and development of parts/products that are toolable and manufacturable, and that function flawlessly in their intended applications. His CAE simulations (FEA, Moldflow, CFD) in product development have consistently predicted accurate results that correlate very well with the actual applications. Mr. Lau applies his knowledge in engineering fundamentals, design guidelines, and CAE simulation to achieve ‘Do It Right the First Time’. This had resulted in projects staying on schedule, on-cost, and on-quality virtually every time. He has trained engineers in many MNC’s, SME’s, and Skills Development Centres, over the years. Mr. Lau is a certified PSBM (HRDF) trainer, as well as a holder in Certified Advanced and Expert Scientific Injection Molding. He also holds US Patent 6853492 Conductive Lens.
Moisture Control for Quality Molded Plastic Parts
Speaker: Alex Lau
Registration Fee: Member: 225 US$
Non-Member: 375 US$
Group (5 Pax): 900 US$
Non-Member: 375 US$
Group (5 Pax): 900 US$
Language: English
Time Length: ~105 Min
To Register: Details & Register
Description: Control of moisture content in the resin is essential for producing quality plastic parts. This is especially so for hygroscopic resins (ABS, nylon, polycarbonate, PET, etc), yet it is an often-overlooked step of the injection molding process. Excess moisture in the resin can show up as splay (or silver streaks) or may manifest itself later as brittle broken parts. The former can be visually caught and rejected, but the latter may make their way into the customer’s hands. And both will hit the bottom line of reduced profits. Moisture control starts with properly drying the resins, but the only real step that matters is the measurement of the moisture content after drying. And this is where many molders are lacking. This KnowHow Webinar will present the defects caused by excessive moisture, the proper steps of drying, cases from industry demonstrating the real missteps of controlling moisture content, and case studies of real defects.
Speaker: Mr. Alex Lau holds a B.Sc. in Mechanical Engineering from University of Manchester, and has worked in the R&D’s of several prominent global MNC’s (Novatel Calgary, NORTEL Calgary, Motorola Penang, Agilent Penang, and Seagate Seremban). He has >30 years experience, specializing in the design and development of parts/products that are toolable and manufacturable, and that function flawlessly in their intended applications. His CAE simulations (FEA, Moldflow, CFD) in product development have consistently predicted accurate results that correlate very well with the actual applications. Mr. Lau applies his knowledge in engineering fundamentals, design guidelines, and CAE simulation to achieve ‘Do It Right the First Time’. This had resulted in projects staying on schedule, on-cost, and on-quality virtually every time. He has trained engineers in many MNC’s, SME’s, and Skills Development Centres, over the years. Mr. Lau is a certified PSBM (HRDF) trainer, as well as a holder in Certified Advanced and Expert Scientific Injection Molding. He also holds US Patent 6853492 Conductive Lens.
Critical Finite Element Analysis (FEA) for Plastic Parts
Speaker: Alex Lau
Registration Fee: Member: 225 US$
Non-Member: 375 US$
Group (5 Pax): 900 US$
Non-Member: 375 US$
Group (5 Pax): 900 US$
Language: English
Time Length: ~95 Min
To Register: Details & Register
Description: Plastic parts, with their capability for complex shapes, find many structural applications in many high-end industries like aircraft, automotive, and medical. FEA is a very useful tool to predict their structural performance in complicated applications. However, several critical considerations are mandatory if one seeks accurate predictions of stress, displacement, force, etc. This is because plastics do not behave like metals, for which FEA was originally developed for. This webinar will demonstrate the advantages of those critical considerations versus the traditional linear approach.
Speaker: Mr. Alex Lau holds a B.Sc. in Mechanical Engineering from University of Manchester, and has worked in the R&D’s of several prominent global MNC’s (Novatel Calgary, NORTEL Calgary, Motorola Penang, Agilent Penang, and Seagate Seremban). He has >30 years experience, specializing in the design and development of parts/products that are toolable and manufacturable, and that function flawlessly in their intended applications. His CAE simulations (FEA, Moldflow, CFD) in product development have consistently predicted accurate results that correlate very well with the actual applications. Mr. Lau applies his knowledge in engineering fundamentals, design guidelines, and CAE simulation to achieve ‘Do It Right the First Time’. This had resulted in projects staying on schedule, on-cost, and on-quality virtually every time. He has trained engineers in many MNC’s, SME’s, and Skills Development Centres, over the years. Mr. Lau is a certified PSBM (HRDF) trainer, as well as a holder in Certified Advanced and Expert Scientific Injection Molding. He also holds US Patent 6853492 Conductive Lens.
Fatigue Failure of Molded Plastic Parts and Design Guidance
Speaker: Alex Lau
Registration Fee: Member: 225 US$
Non-Member: 375 US$
Group (5 Pax): 900 US$
Non-Member: 375 US$
Group (5 Pax): 900 US$
Language: English
Time Length: ~75 Min
To Register: Details & Register
Description: Fatigue failure of molded plastic parts is the breakage of the part after repeated application of a load (whether a force load or a displacement load) that induced stresses on the parts. The induced stress at which fatigue failure occurs is significantly lower than the Yield Strength of the material. Plastics are more prone to fatigue failure than metals. Just as with creep failure, fatigue failure only manifests itself after time has passed and it is usually the customer who experiences it. This has the potential for costly recalls, returns, rework, scrap, warranty claims, loss of revenue, legal liabilities, etc. And the correction will take a long time to implement because it likely involves a redesign, re-tool and mold, re-test, which prolongs the customer’s pain. Merely replacing the failed part with one of the same vintage will repeat the pain. This webinar will describe and discuss: • What are fatigue failures, along with some examples. • How to identify fatigue failures. • How did fatigue failures happen? • How to design around fatigue failures.
Speaker: Mr. Alex Lau holds a B.Sc. in Mechanical Engineering from University of Manchester, and has worked in the R&D’s of several prominent global MNC’s (Novatel Calgary, NORTEL Calgary, Motorola Penang, Agilent Penang, and Seagate Seremban). He has >30 years experience, specializing in the design and development of parts/products that are toolable and manufacturable, and that function flawlessly in their intended applications. His CAE simulations (FEA, Moldflow, CFD) in product development have consistently predicted accurate results that correlate very well with the actual applications. Mr. Lau applies his knowledge in engineering fundamentals, design guidelines, and CAE simulation to achieve ‘Do It Right the First Time’. This had resulted in projects staying on schedule, on-cost, and on-quality virtually every time. He has trained engineers in many MNC’s, SME’s, and Skills Development Centres, over the years. Mr. Lau is a certified PSBM (HRDF) trainer, as well as a holder in Certified Advanced and Expert Scientific Injection Molding. He also holds US Patent 6853492 Conductive Lens.
Design for Manufacturing & Assembly (DFMA) for Molded Plastic Parts
Speaker: Alex Lau
Registration Fee: Member: 225 US$
Non-Member: 375 US$
Group (5 Pax): 900 US$
Non-Member: 375 US$
Group (5 Pax): 900 US$
Language: English
Time Length: ~90 Min
To Register: Details & Register
Description: DFMA = DFM + DFA, respectively Design for Manufacturing, and Design for Assembly. DFM looks at the cost for manufacturing plastic parts individually. DFA looks at the cost of assembling those parts together to make the finished product. Together DFMA is the philosophy of making the parts and products to be lean from the very beginning. This avoids expensive engineering changes later. It also makes for a lower cost, better reliability, and better-quality product. DFMA pulls in the participation of all the relevant departments (internal and external) at the design stage, where 70 to 80% of a product’s total cost is established. The material to be used, the type of manufacturing process, the assembly processes are all defined at the design stage. Without DFMA bad design decisions may be carried over into the mass production stage where costs and risks to start over are very high. This webinar will examine the application of DFMA philosophy to molded plastic parts – how to produce the molded parts productively, and how plastic parts can incorporate many features that ease assembly into the finished product.
Speaker: Mr. Alex Lau holds a B.Sc. in Mechanical Engineering from University of Manchester, and has worked in the R&D’s of several prominent global MNC’s (Novatel Calgary, NORTEL Calgary, Motorola Penang, Agilent Penang, and Seagate Seremban). He has >30 years experience, specializing in the design and development of parts/products that are toolable and manufacturable, and that function flawlessly in their intended applications. His CAE simulations (FEA, Moldflow, CFD) in product development have consistently predicted accurate results that correlate very well with the actual applications. Mr. Lau applies his knowledge in engineering fundamentals, design guidelines, and CAE simulation to achieve ‘Do It Right the First Time’. This had resulted in projects staying on schedule, on-cost, and on-quality virtually every time. He has trained engineers in many MNC’s, SME’s, and Skills Development Centres, over the years. Mr. Lau is a certified PSBM (HRDF) trainer, as well as a holder in Certified Advanced and Expert Scientific Injection Molding. He also holds US Patent 6853492 Conductive Lens.
30 Best Practices for Quality Molded Plastic Parts
Speaker: Alex Lau
Registration Fee: Member: 225 US$
Non-Member: 375 US$
Group (5 Pax): 900 US$
Non-Member: 375 US$
Group (5 Pax): 900 US$
Language: English
Time Length: ~120 Min
To Register: Details & Register
Description: A good quality molded plastic part is one that can be molded with high yield and performs flawlessly in its intended application. To this end there are certain best practices to be adhered to by the part designer as well as the toolmaker/molder.
In the preliminary stages of part design there is great advantage to leveraging the knowledge and experience of the engineering team of the toolmaker/molder who have likely “seen it all”. This is in contrast to designing in a silo and passing down design features that need costly modifications after mold trials. It is just as easy to design a part feature that will mold well, as it is to design a bad feature that will hamper molding, eg. insufficient draft angle. To do justice to a well designed part, there are also best practices for the toolmaker/molder to adhere to. Here are 30 best practices to get good quality molded plastic parts.
Speaker: Mr. Alex Lau holds a B.Sc. in Mechanical Engineering from University of Manchester, and has worked in the R&D’s of several prominent global MNC’s (Novatel Calgary, NORTEL Calgary, Motorola Penang, Agilent Penang, and Seagate Seremban). He has >30 years experience, specializing in the design and development of parts/products that are toolable and manufacturable, and that function flawlessly in their intended applications. His CAE simulations (FEA, Moldflow, CFD) in product development have consistently predicted accurate results that correlate very well with the actual applications. Mr. Lau applies his knowledge in engineering fundamentals, design guidelines, and CAE simulation to achieve ‘Do It Right the First Time’. This had resulted in projects staying on schedule, on-cost, and on-quality virtually every time. He has trained engineers in many MNC’s, SME’s, and Skills Development Centres, over the years. Mr. Lau is a certified PSBM (HRDF) trainer, as well as a holder in Certified Advanced and Expert Scientific Injection Molding. He also holds US Patent 6853492 Conductive Lens.
Warpage Failure of Molded Plastic Parts and Guidance
Speaker: Alex Lau
Registration Fee: Member: 225 US$
Non-Member: 375 US$
Group (5 Pax): 900 US$
Non-Member: 375 US$
Group (5 Pax): 900 US$
Language: English
Time Length: ~80 Min
To Register: Details & Register
Description: Warpage of a molded plastic part comes down to uneven shrinkage of the part while it is cooling down to room temperature after ejection. Warpage results in a part that is not of the intended shape, and is one of the most common failures. Understanding the causes for the uneven shrinkage is complicated but it is essential. Those causes are material, design, mould, and processing. Using a jig to hold the shape of the part during cooling, after ejection, is not recommended as it can have disastrous results later. This webinar will discuss the various causes of uneven shrinkage and how to mitigate them. A case study will be presented to demonstrate the use of Conformal Cooling to reduce warpage.
Speaker: Mr. Alex Lau holds a B.Sc. in Mechanical Engineering from University of Manchester, and has worked in the R&D’s of several prominent global MNC’s (Novatel Calgary, NORTEL Calgary, Motorola Penang, Agilent Penang, and Seagate Seremban). He has >30 years experience, specializing in the design and development of parts/products that are toolable and manufacturable, and that function flawlessly in their intended applications. His CAE simulations (FEA, Moldflow, CFD) in product development have consistently predicted accurate results that correlate very well with the actual applications. Mr. Lau applies his knowledge in engineering fundamentals, design guidelines, and CAE simulation to achieve ‘Do It Right the First Time’. This had resulted in projects staying on schedule, on-cost, and on-quality virtually every time. He has trained engineers in many MNC’s, SME’s, and Skills Development Centres, over the years. Mr. Lau is a certified PSBM (HRDF) trainer, as well as a holder in Certified Advanced and Expert Scientific Injection Molding. He also holds US Patent 6853492 Conductive Lens.
Technical Discussion : Quality Molded Plastic Parts Design
Speaker: Alex Lau
Registration Fee: Member: 225 US$
Non-Member: 375 US$
Group (5 Pax): 900 US$
Non-Member: 375 US$
Group (5 Pax): 900 US$
Language: English
Time Length: ~145 Min
To Register: Details & Register
Description: This is the first edition of KnowHow Q &A Session focusing on Quality Molded Plastic Parts Design. Participants asked followed questions on various issues related to design and failures of molded plastic parts. Mr. Alex Lau addressed all the real questions/ issues raised by participants, which was held on 2 April 2021. The questions/issues addressed in this Q&A session are: # How does under-cooling of the molds cause warpage?; # I had dried the resins and checked the moisture content to specification before molding, why did the parts break in one batch of molding but not another batch?; # I’ve used FEA, found that it’s not accurate. Any suggestions why?; # Can I allow my toolmaker to add the draft angles for me, since he’s very familiar with the requirements?; # Should I use ribs to help reduce warpage?; # If I use FEA to accurately calculate the stress, and considered creep performance of plastics, the part should last a long time?; # What is nonlinear FEA?; # Theoretically, to eliminate warpage, can I leave the part in the mold until it cools down to room temperature?; # I measured the moisture content when the bags of resins were received. I rejected those that exceeded the limits, then used the remainder without further moisture content checks. Is this ok?; Can I have zero draft angle on some features?; Nonlinear FEA takes too long. Can I use linear FEA for fast answers?; The molded part broke but I don’t see those fatigue ‘beach marks’ on the surface of the break. Why?; # Can DFMA help to reduce cycle time of molding?; # I used hand calculation to determine the working stress in the plastic structural part. Is this good enough? # My toolmaker does the Moldflow analysis for me. Why not continue as is?; # What is MFR?; # I practice DFM and FMEA quality processes in my company. Why didn’t they identify potential fatigue failures?; # Why are the glass-reinforced plastics more resistant to creep?; # I don’t have an FEA analyst in my company. Can I out-source the job?; # I’ve done nonlinear FEA with mesh refinement. The production part was tested and its performance correlated with the FEA predicted results, all well and good. Some weeks later the production part still broke, how come?; If the molded part is not compliant to UL Flammability can I change to another grade that is compliant?; For a desiccant dryer machine can I set to -20C dew point?; My FEA reseller did not tell me about nonlinear FEA. Why was that?; My designs are out-sourced. How can I be sure the out-sourced designer had taken fatigue failure into account?; I used a jig to hold the warped part straight during cooling after ejection. Fortunately, I have not had problems with the parts warping back at a later time. Why was that?; In a plastic part that failed by deformation or breakage, why not just change to a stronger plastic?; Can I modify the gates, molding parameters, temperatures, etc. to eliminate fatigue failure?; Can cosmetic defects be removed by adjusting the molding parameters?; Is Conformal Cooling expensive?; How good is the Boothroyd & Dewhurst DFMA software?
Speaker: Mr. Alex Lau holds a B.Sc. in Mechanical Engineering from University of Manchester, and has worked in the R&D’s of several prominent global MNC’s (Novatel Calgary, NORTEL Calgary, Motorola Penang, Agilent Penang, and Seagate Seremban). He has >30 years experience, specializing in the design and development of parts/products that are toolable and manufacturable, and that function flawlessly in their intended applications. His CAE simulations (FEA, Moldflow, CFD) in product development have consistently predicted accurate results that correlate very well with the actual applications. Mr. Lau applies his knowledge in engineering fundamentals, design guidelines, and CAE simulation to achieve ‘Do It Right the First Time’. This had resulted in projects staying on schedule, on-cost, and on-quality virtually every time. He has trained engineers in many MNC’s, SME’s, and Skills Development Centres, over the years. Mr. Lau is a certified PSBM (HRDF) trainer, as well as a holder in Certified Advanced and Expert Scientific Injection Molding. He also holds US Patent 6853492 Conductive Lens.
Contact for Assistance :
THAILAND
Tel: +66-89-489 0525
Email: peram.technobiz@gmail.com
WhatsApp/WeChat: +66-89-489 0525 (messages only)
USA
Tel: +1-856-981 4381
Contact Address
KnowHow Webinars
TechnoBiz Communications Co., Ltd
2521/27, Lardprao Road, Khlongchaokhunsingha
Wangthonglang, Bangkok 10310 THAILAND
Tel: +66-2-933 0077 Fax: +66-2-955 9971
WhatsApp: +66-89-489 0525